Note: The clutch is removed upwards with the DSG removed. When installing a new clutch, it is necessary to determine and adjust the positions of the bearings, after which the clutch is pressed against the input shaft. After installing the clutch to the stop, it should be slightly pulled up. Couplings of different designs can be used: old and new; only a new design clutch is supplied as a spare part.
Attention: A self-adjusting clutch is used, which can be adversely affected by vibrations. Therefore, do not let the clutch fall, do not release it when installing in the DSG.
Removing
1. Remove DSG (see Section 4). Don't remove the block "Mechatronic".
2. Remove caps from both vents (1 and 4 in illustration 1.5) and plug them so that working fluids do not spill out.
3. Attach the DSG with the clutch up and remove the hub circlip (arrow on resist illustrations).
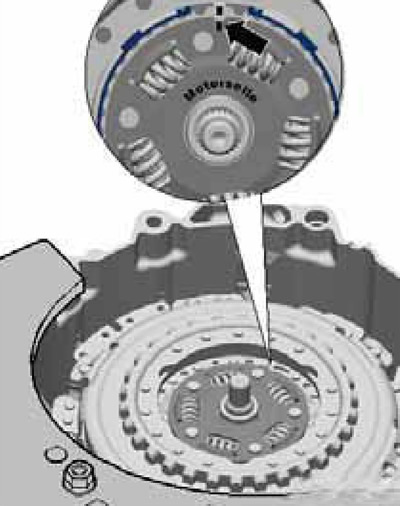
5.3 Hub circlip
4. Remove the hub using hook N°3438 and a screwdriver (see resist. illustration).
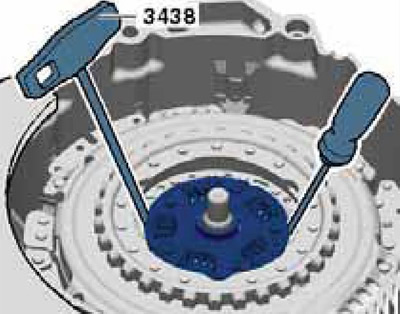
5.4 Removing/installing the hub
5. Remove the clutch retaining ring (see resist. illustration). It is possible that the ring is very tight - the reason may be a strong pressure on it from the clutch.
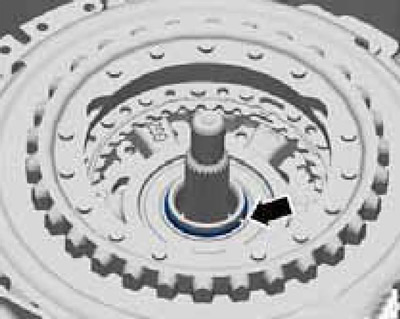
5.5 Clutch retaining ring
6. If the ring cannot be removed, apply slight pressure on the clutch. Never strike the clutch or shaft. To press in the clutch, use the fixture illustrations. The distances on both sides must first be aligned, e.g. with washers (IN), and should be approximately 15 mm. After removal, the clutch retaining ring must be replaced.
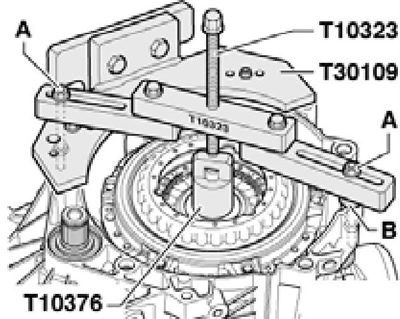
5.6 Pressing in the clutch
7. Screw puller T10373 onto the clutch and pull out the clutch together with the puller (see resist. illustration).

5.7 Removing the clutch
8. Remove the small clutch engagement bearing and the large clutch lever (see resist. illustration).
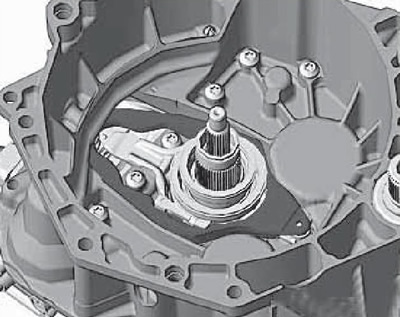
5.8 Removing the large clutch lever
9. Turn out bolts and remove the small lever of inclusion of coupling (see resist. illustration).
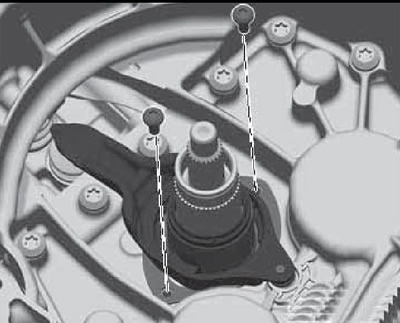
15.9 Removing the small clutch lever
10. Remove the clutch lever holder (see resist. illustration).
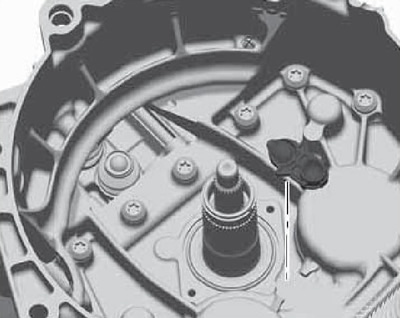
5.10 Removing the lever holder
Old clutch installation
11. If the clutch engagement bearings, clutch engagement levers or their holders are replaced, then before installing the clutch, it is necessary to adjust the position of the clutch engagement bearings, as described in the appropriate subsection below.
12. Do not lubricate anything when installing.
13. Install the plastic clutch lever holder (see illustration 5.10).
14. If the small lever is removed, install it together with the guide sleeve and make sure that the lever fits correctly. Fix the lever by screwing in two new bolts of its fastening (8 Nm, then tighten to 90°), - see illustration 5.9. Check the arm rest and the entire mechanism for the bearings - they must be dry and free of grease. If necessary, clean everything with a cloth.
15. If not already installed, insert the large clutch lever, see illustration 5.8. Make sure both levers are seated correctly. Insert the large bearing and check for proper seating.
16. Insert the small bearing. Due to the presence of four grooves, the small bearing is installed in only one position. Check bearing position by turning (see resist. illustration), - the grooves must fit into the holder.
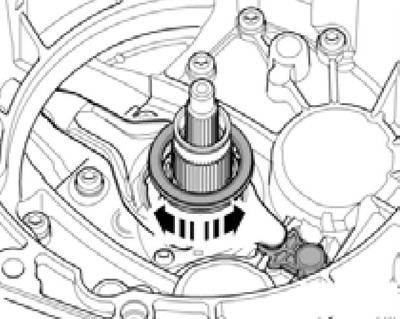
5.16 Checking the fit of the bearing
17. Both matched shims (arrows on resist. illustrations) must be located on both bearings. The shim for the K1 clutch is mounted on the large bearing, and the shim for the K2 clutch is mounted on the small bearing. The washers can be fixed with three drops of AMV195 KD1 01 glue to prevent them from slipping when the clutch is installed.
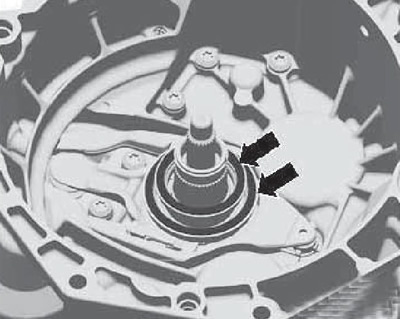
5.17 Shims
18. Turn back the puller spindle T10373 and insert the clutch on the puller into the DSG (see illustration 5.7), without letting it fall. A fall may cause a malfunction of the automatic clutch adjustment mechanism.
19. Push the clutch all the way in as described in paragraph 6. Place your hand on the clutch as you push it in and you will feel a slight vibration indicating that the clutch is pressed into its seat. You can also feel that the clutch is inserted all the way.
20. Look at the clearance of the clutch retaining ring (see illustration 5.5), - it has different width. The narrower gap should be at the top. Insert a new retaining ring. If this was done, then the clutch is correctly inserted all the way,
21. Insert the hub with the inscription "Motorseite" to the engine. The hub has a large tooth. therefore, it can only be installed in one position. On the side of the hub with the inscription "Motorseite" opposite her large tooth there is a mark that must match the mark on the clutch housing (see illustration 5.3). Insert the hub circlip so that its gap faces the lug on the clutch.
22. Rotate the clutch by hand from side to side and make sure that the small clutch lever does not move up and down. Moving the lever indicates that the shim for the K2 clutch is not seated correctly. In this case, remove the clutch and reinstall it. paying special attention to the washers: they must be correctly inserted into the respective bearings and must not be damaged.
23. Remove the plugs and replace the breather caps. Install the DSG and use the scan tool to apply basic settings to it.
Installing a New Design Clutch
24. If a new design clutch or its control parts is replaced (levers, their holders and bearings), then before installing the clutch, it is necessary to adjust the position of the clutch engagement bearings, as described in the appropriate subsection below. The shim for the K1 clutch is mounted on the large bearing, and the shim for the K2 clutch is mounted under the small bearing.
25. Do not lubricate anything when installing.
26. Install the plastic clutch lever holder (see illustration 5.10).
27. Install the small lever with the retainer. The sleeve with its retaining plate can only be installed in one position. Make sure the lever is seated correctly and tighten the two new lever mounting bolts (8 Nm, then tighten to 90°), - see resist. illustration. Check the arm rest and the entire mechanism for the bearings - they must be dry and not lubricated. If necessary, clean everything with a cloth.
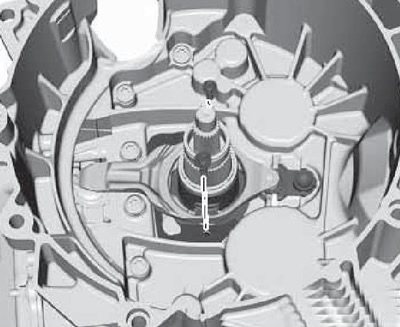
5.27 Small clutch lever bolts
28. Insert large clutch lever (for clutch "K1"), see illustration 5.8. Make sure both levers are seated correctly.
29. Install the small bearing (And on the opposite illustrations) with required shim (IN). The washer should be under the small bearing, so install it first. Due to the presence of four grooves, the small bearing is installed in only one position. If the clutch is replaced, the small bearing must also be replaced. Check the position of the bearing by turning it.
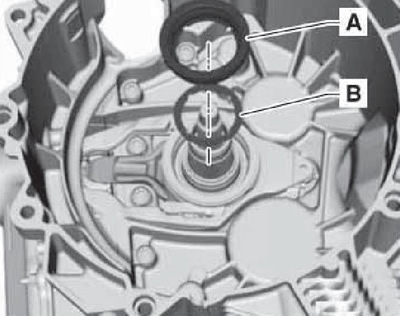
5.29 Small bearing (A) with shim (IN)
30. Fasten the washer (And on the opposite illustrations) three drops of AMV195 KD1 01 glue in the places indicated by the arrows - this will prevent the washer from slipping when installing the clutch.
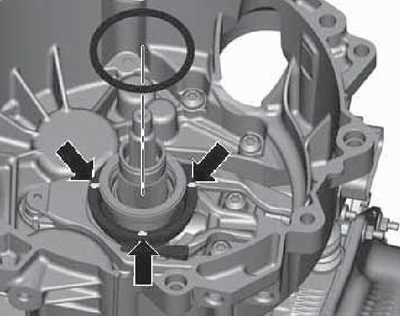
5.30 Fixing the shim
Note: Large washer - for clutch "K1", and small - for clutch "K2".
31. Follow the steps described in paragraphs 18-20.
32. In order for the clutch to take up its working position, turn it against the puller T10373 by hand (see resist. illustration). The clutch moves against the retaining ring. Pressing causes the clutch to be set on the bottom of the shaft. The clutch should be pulled up just enough to touch the circlip.
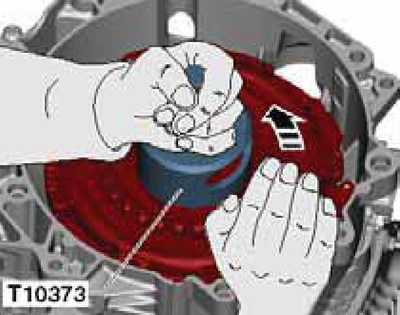
5.32 Bringing the clutch into working position
33. Follow the steps described in paragraphs 21-23.
New Design Clutch Bearing Adjustment
34. In general terms, the position of the bearings is comparable to the clutch play on a conventional manual transmission. The DSG has approvals in the gearing system and in the DSG itself. There are also tolerances in the double clutch, which must be taken into account separately when adjusting. When adjusting, all necessary dimensions are first measured to determine the required thickness of the shim. Adhesion tolerances are then determined and included in the calculations (washer thickness determined by DSG and clutch tolerances).
35. First determine the size (B on resist. illustrations), which is required for both clutches, and then the dimensions (A1) And (A2).
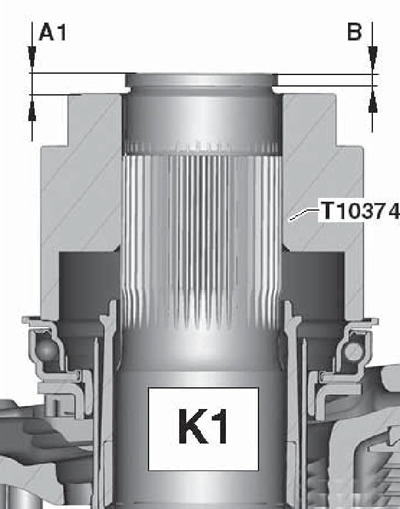
5.35a Coupling dimensions "K1"
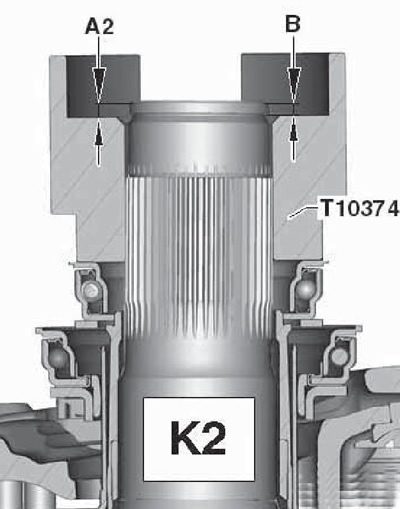
5.35b Coupling dimensions "K2"
36. Install the clutch parts to the large lever (see subsection above), do not install the small bearing and any washers.
37. Install the outer input shaft retaining ring (see resist. illustration).
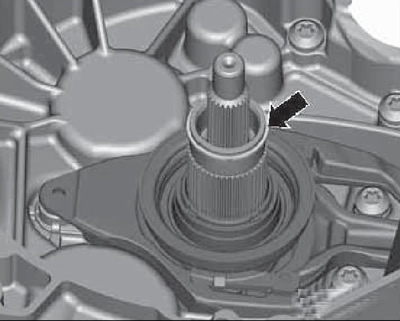
5.37 External input shaft circlip
38. Place a straight ruler T40100 on the clutch housing and do not move it between measurements. Mount the depth gauge and zero it at the distance to the edge of the outer input shaft (see resist. illustration). Measure the distance to the retaining ring and record the result (B in illustrations 5.35a-b). Repeat the measurement on the diametrically opposite side of the outer input shaft and calculate the arithmetic mean (IN), which will be used in further calculations, i.e. Add up both results and divide the sum in half.
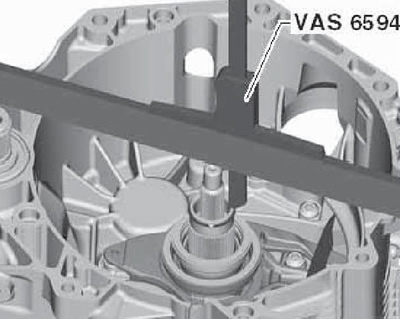
5.38 Measuring the distance to the edge of the outer input shaft
39. Remove the outer input shaft circlip again.
40. Start the calculation with the clutch washer "K1" (see paragraphs 40-43). Place measuring block T10374 on the large bearing (see resist. illustration) 51.81 mm high and push it in while turning. In this way, the rotation of the bearing can be observed and the measuring unit fits correctly on the bearing.
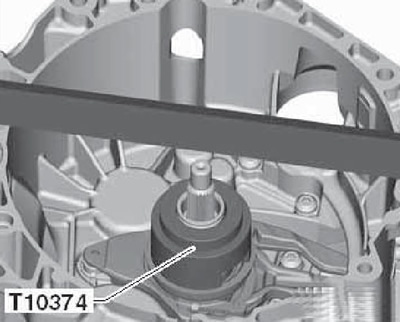
5.40 Mounting the measuring unit on a large bearing
41. Mount the depth gauge to the top of the outer input shaft, zero it, and then measure the distance (A 1 in illustration 5.35a) up to the upper plane of the measuring block (see resist. illustration). Take the measurement twice on each of the two diametrically opposite sides and calculate the arithmetic mean of the A1 size.
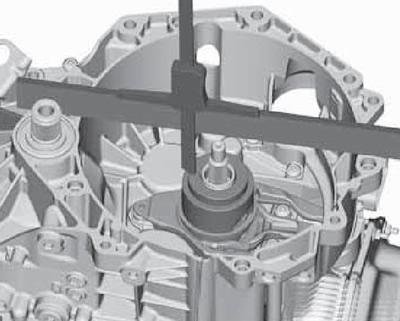
5.41 Sizing "A1"
42. Subtract dimension B from dimension A1 and add the height of the measuring block to the resulting difference (51.81 mm), - you get the size, which means how deep the bearing is seated inside the DSG at the moment. The bearing seating depth should always be 50.08 mm. To calculate the current clutch clearance K1, subtract the required depth from the current bearing installation depth (50.08 mm).
43. Now the tolerance indicated on the new clutch is entered into the calculation of the thickness of the shim (see resist. illustration), - it can be from -0.40 to +0.40 mm. To calculate the thickness of the K1 clutch shim, add the K1 clutch tolerance to the current clearance of the K1 clutch. Washers are available in thicknesses from 0.8 to 2.8 mm in 0.2 mm increments. With a calculated washer thickness between 0.31 and 0.90 mm, select a 0.8 mm washer; at 0.91:1.10 - 1.0 mm; at 1.11 + 1.30 - 1.2 mm, etc. With a calculated thickness between 2.71 and 3.30 mm, select a 2.8 mm washer. Do not install the matched washer yet.
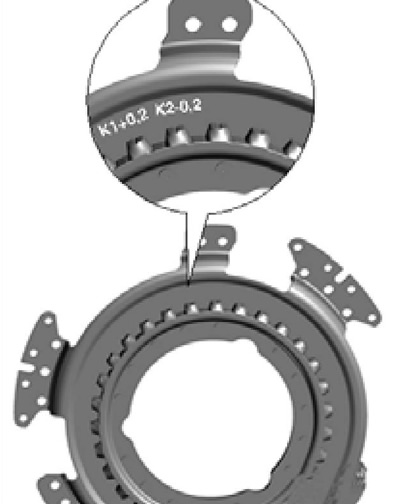
5.43 Specification of tolerances on the clutch
44. Calculate the thickness of the shim for the K2 clutch (see paragraphs 45-48).
45. Without installing any washers, install the small bearing (see subsection above). Due to the presence of four grooves, the small bearing is installed in only one position. Check the position of the bearing by turning it on the input shaft.
46. Mount the T10374 gauge block on the small bearing with the large slots up, install the depth gauge to the top of the outer input shaft, zero it, and then measure the distance (A2 in Illustration 5.35b) up to the upper plane of the measuring block (see resist. illustration). Take the measurement twice on each of the two diametrically opposite sides and calculate the arithmetic mean of the A2 size.
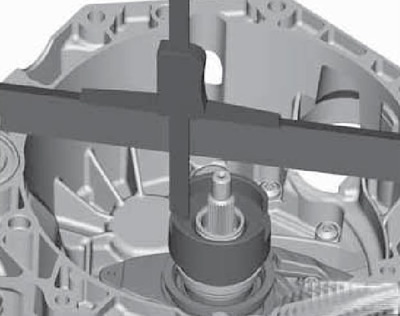
5.46 Sizing "A2"
47. Subtract dimension B from dimension A2 and add to the resulting difference the height of the measuring block along the inside (36.20 mm), - you get the size, which means how deep the bearing is seated inside the DSG at the moment. The bearing seating depth must always be 34.35 mm. To calculate the current clutch clearance K2, subtract the required depth from the current bearing installation depth (34.35 mm).
48. Now the tolerance indicated on the new clutch is entered into the calculation of the thickness of the shim (see illustration 5.43), - it can be from -0.40 to +0.40 mm. To calculate the thickness of the K2 clutch shim, add the K2 clutch tolerance to the current clearance of the K2 clutch. The selection of the washer, depending on the result of the calculations, is carried out in the same way as for the K1 clutch. Do not install the matched washer yet.
49. Install the clutch with matched washers as described in the subsection above.
Old design clutch bearing adjustment
50. Remove the previously installed shims from the bearings, clean the seating surfaces on the bearings.
51. Select 1.4 mm thick washers from the supplied washers and place them on the bearings (see illustration 5.17).
52. Select a large washer for the clutch bearing K1, as described in paragraphs 53-56.
53. Remove the small bearing again along with the 1.4mm washer.
54. Place measuring block T10374 on the large bearing (see illustration 5.55) and push it in while turning. In this way, the rotation of the bearing can be observed, and the measuring unit fits correctly on the bearing (the bearing must rotate with the washer).
55. Lay the T40100 ruler on the clutch housing and measure the distance from the ruler to the edge of the input shaft with a depth gauge (see resist. illustration). Then twice (at two opposite points) measure the distance from the ruler to the upper plane of the T10374 measuring block, calculate the average value from these two measurements, then subtract from it the distance to the edge of the input shaft - this will be the thickness of the desired shim. Washers are available in thicknesses from 0.8 to 2.8 mm in 0.2 mm increments. With a calculated washer thickness between 0.71 and 0.90 mm, select a 0.8 mm washer; at 0.91:1.10—1.0 mm, etc. With a calculated thickness between 2.71 and 2.90 mm, select a 2.8 mm washer.
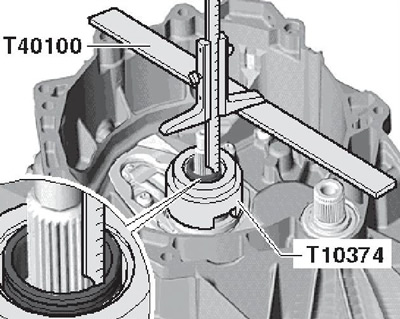
5.55 Measuring the distance from the ruler to the edge of the input shaft
56. If necessary, replace the 1.4 mm washer used in the measurements with a matched washer. Note: When adjusting, only one shim should be installed on all bearings.
57. Select a small washer for the K2 clutch bearing as described in paragraphs 58-59.
58. Remove the large lever together with the K1 clutch bearing. Install the small bearing with a 1.4 mm thick washer. Due to the presence of four grooves, the small bearing is installed in only one position. Check bearing position by turning (see illustration 5.16), - the grooves must fit into the holder.
59. Place measuring block T10374 on the small bearing (see illustration 5.55), measure and calculate the thickness of the washer for the K2 clutch bearing in the same way as indicated in paragraph 55.
60. If necessary, replace the 1.4 mm washer used in the measurements with a matched washer.
Note: When adjusting, only one shim should be installed on all bearings.