Cleaning
1. Remove all attachments and components from the unit, as well as electrical sensors and switches. For a full-scale cleaning, it is also necessary to remove the squeeze plugs of the water galleries - drill small holes in the plugs, screw self-tapping screws into them and, grasping the screw heads with pliers, remove the plugs from the block.
2. Scrape off all traces of the old gasket material and sealant from the mating surfaces of the block. Be careful not to damage the gasket/seal surfaces.
3. Remove all oil gallery plugs (where they are provided). The plugs are very tight and may need to be drilled out and re-threaded with a tap. When assembling the engine, the replacement of plugs is mandatory.
4. If the crankcase is very dirty, you will have to resort to steam cleaning. After returning the block from cleaning, it is necessary to clean the oil flows and galleries again. Rinse all internal cavities of the block with warm water. Continue flushing until clean water flows out of the holes. Dry the block thoroughly, then lightly lubricate its mating surfaces and cylinder mirrors with oil to prevent corrosion. If you have access to a compressed air source, use it to speed up the drying process and blow out openings, channels and galleries.
Attention! Wear protective goggles when using compressed air!
5. If the engine crankcase is not too dirty, it will be enough to wash it with hot soapy water using a stiff brush. You should not try to save time on washing the block - take this procedure with all responsibility. Regardless of the cleaning method chosen, as a result of it, all oil holes and channels should be absolutely clean, and the block should be thoroughly dried. To prevent corrosion, lightly lubricate the cylinder mirrors with oil.
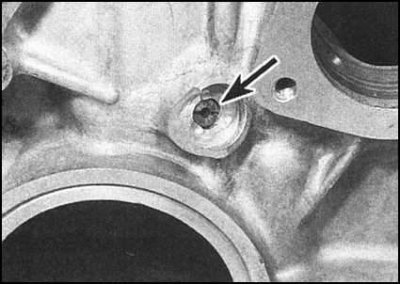
6. All mounting holes in the block are required "drive away" with a suitable tap, carefully removing corrosion products, old sealant and other deposits from the threads. In addition, such "sweep" will help repair damaged coils. If possible, blow holes with compressed air to remove chips and debris.
Attention! All traces of grease and solvent must be completely removed from the blind holes to prevent hydraulic pressure destroying the block casting when the bolts are tightened.
7. Lubricate the new oil gallery plugs with a suitable sealant and screw them into their holes in the block. Tighten the plugs firmly.
8. If you are not going to assemble the engine immediately, wrap the unit in a clean plastic bag. Do not forget to also take care of the protection of mating surfaces and cylinder mirrors from corrosion.
Examination
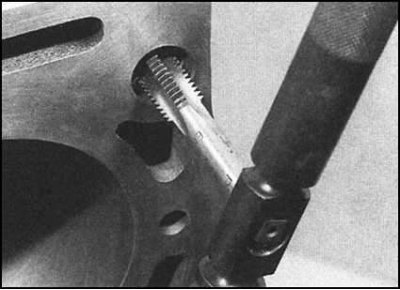
1. Inspect the block casting for cracks and corrosion. Check for stripped threads in any of the mounting holes. If there were suspicions of internal coolant leaks, it may make sense to contact a car service specialist, asking them to perform a thorough check of the condition of the unit using special equipment. If necessary, repair or replace the unit.
2. Remove the cylinder liners and check their mirrors for scratches and burrs. In order to maintain manufacturing tolerances, sleeves are produced in three size groups. The corresponding marking is applied to the wall of each of the sleeves.
3. For a more accurate assessment of the degree of wear of the sleeves, it is necessary to measure their diameters at several points. Enter the bore gauge into the first cylinder liner and measure its diameter in three different sections parallel to the crankshaft axis. One measurement is made in the upper part of the sleeve, directly under the edge of the stepped wear shoulder, the second - in the central part of the sleeve and the third - immediately above its lower cut. Measurements are made in two planes - parallel and perpendicular to the axis of the crankshaft.
4. Compare measurement results with requirements Specifications. If any of the results are out of range, the corresponding sleeve must be replaced.
5. To determine the clearance of the pistons in the cylinder liners, it is necessary to subtract from the diameter of the sleeve the diameter of the piston, measured along its skirt (see Section Removal, condition check and installation of connecting rod and piston assemblies).
6. Alternatively, fit the piston into a suitable sleeve and use a blade-type feeler gauge to measure its seat play. The piston must be inserted into the sleeve in its normal position, and the play is measured along one of its thrust surfaces, directly above the lower cut of the sleeve.
7. If the clearance exceeds the specified Specifications acceptable value, the piston must be replaced. If the piston sticks at the bottom of the stroke, with a gradual loosening of the fit as it moves up, then there is a liner taper. Jamming of the probe blades when it is displaced along the perimeter of the generatrix of the piston surface indicates the ovality of the sleeve.
8. Repeat the procedure, evaluating the condition of the sleeves of each of the cylinders.
9. In case of revealing signs of excessive wear or damage to the mirrors, defective sleeves must be replaced.
10. Sleeves should be installed as replacement ones, only of the same size group as the failed ones. The same applies to pistons. In this case, the size of the pistons must correspond to the size of the sleeves in the group. The corresponding marking is applied to the walls of the sleeves and the bottom of the pistons.
11. If the degree of wear of the mirrors is low, it will be enough just to replace the piston rings.
12. The mirrors of the sleeves are subject to honing in order to ensure the correct fit of the new piston rings on them.
13. A special tool is required to perform the honing procedure (hone), which allows you to apply a uniform dashed pattern in the form of a grid on the surface of the mirror. Such a uniform "coarsening" The mirror ensures the quality of the running-in of the piston rings and guarantees the proper tightness of the fit of the pistons in the liners. Two types of hones are available, both designed to be used with an electric drill. hone type "bottle brush" represents a rigid cylindrical brush with abrasive inserts in a bristle. The more widespread surface hone is equipped with a head in the form of grindstones equipped with spring-loaded legs. The compilers of this manual recommend that novice amateur mechanics use the first type of hone.
Note. If desired, honing can always be entrusted to the specialists of a car service workshop for a very reasonable fee.
14. Prepare one of the types of honing tool described above, an electric drill, a sufficient amount of clean rags, some honing oil, and goggles.
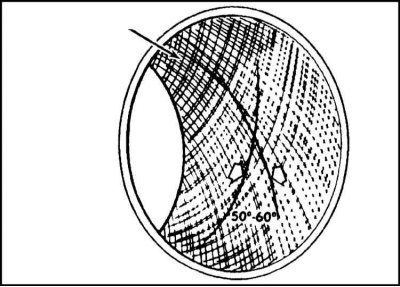
15. Clamp the hone into the drill chuck. Moisten the cylinder bores with honing oil and tuck the hon into the first sleeve, pre-compressing its spring-loaded whetstones (if the nozzle of the second type is used). Turn on the drill and immediately begin to move the nozzle up and down the cylinder, achieving the appearance on the mirror of the cylinder of a uniform dashed pattern in the form of a grid with a diamond-shaped mesh, the sides of which intersect at an angle of about 60°. Some piston ring manufacturers insist on different pattern bar angles - refer to the instructions that came with your new piston ring set.
Attention! Don't forget to wear safety goggles!
16. Spare no oil when honing cylinders. Do not remove more material from the sleeve mirror than is really necessary to achieve the desired result. Do not remove the hone from the sleeve until its rotation finally stops - all this time continue to reciprocate with the drill. After stopping the drill, continue to rotate its chuck in the same direction by hand and remove the nozzle from the cylinder.
17. Wipe the mirror thoroughly with a clean cloth and proceed to honing the next cylinder liner. When finished, wash the cylinder block with hot soapy water to completely remove all traces of abrasive and honing oil. Cleaning can be considered complete when, when the shells are passed over the mirrors with a white cloth soaked in oil, there is no gray stain on the latter.
18. For removal of sleeves turn over the block of cylinders and lay it on wooden blocks. The liners can now be knocked out of the cylinders with a hardwood drift.
19. After all liners are released, lay the cylinder block on its side and remove the liners by hand.
20. Remove the sealing washers from the bases of the sleeves and measure their thickness. Washers of various sizes are produced and by selecting them, the protrusion of the sleeves above the surface of the block is adjusted. Pick up replacement washers for each of the sleeves.
21. The main geometric characteristics of the sleeves are shown in the illustrations. If the sleeves are in good condition and are subject to further use, mark them with adhesive tape for belonging to your cylinder.
- a - Designation of the size class of the sleeve
- b - Inner diameter measurement point
![]() | ![]() |
22. Before installation, thoroughly wipe the mating surfaces of the sleeves and sides, then by processing with fine-grained sandpaper, remove all burrs, scuffs and roughness that can lead to failure of new sealing washers.
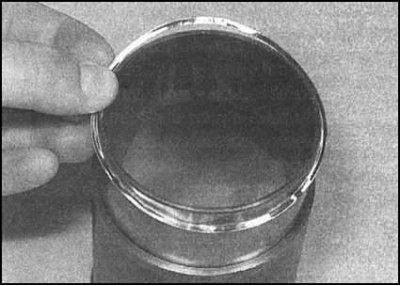
23. Wipe the sleeves thoroughly and install new sealing washers of the required thickness on them. Lubricate the walls of the sleeves with clean engine oil.
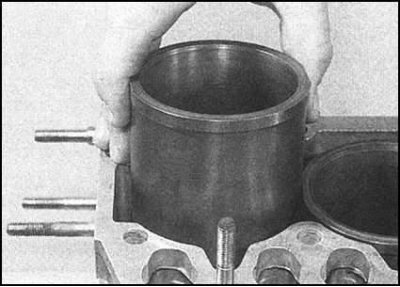
24. When installing old sleeves, make sure that the landing marks applied during dismantling are aligned correctly. Try not to let the sealing washers fall out when the liners are seated in the cylinders. At the first stage, the liners should be pushed into the cylinders by hand until they stop. Next, the sleeves are tapped with a hammer through a wooden block until it stops against the landing hangers.
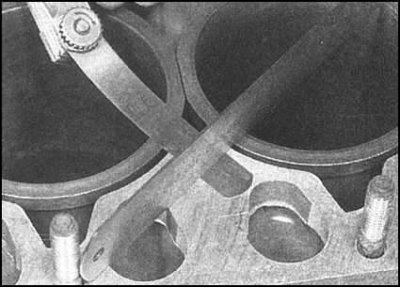
25. Having installed all four sleeves, measure the amount of their protrusion above the plane of the block - use a steel ruler and a blade-type probe. Compare measurement results with requirements Specifications.
26. If necessary, remove the incorrectly seated sleeve and replace the sealing washer on it. Washers are available in thicknesses of 0.10, 0.12 and 0.14 mm.
27. After replacing the washer, install the sleeve and recheck the amount of protrusion.
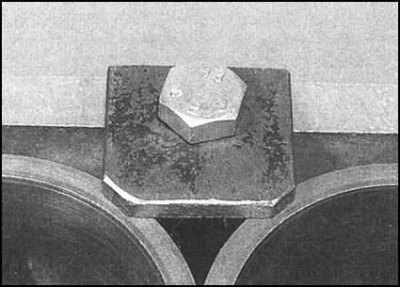
28. Having finished adjusting the fit of the sleeves, temporarily fix them in the cylinders with special rectangular washers
Engines 1.6 l and diesel
1. Visually inspect the block casting for cracks and corrosion. Check for stripped threads in any of the mounting holes. If there were suspicions of internal coolant leaks, it may make sense to contact a car service specialist, asking them to perform a thorough check of the condition of the unit using special equipment. If necessary, repair or replace the unit.
2. Check up mirrors of cylinders on presence of scratches and scuffs. If such defects are found, the condition of the corresponding pistons should be checked (see Section Removal, condition check and installation of connecting rod and piston assemblies). Defects that are in the initial stage of development can be eliminated at this stage by turning the block in a car service workshop.
3. For a more accurate assessment of the degree of wear of the cylinders, it is necessary to measure their diameters at several points. Enter the bore gauge into the first cylinder and measure its diameter in three different sections parallel to the axis of the crankshaft. One measurement is made in the upper part of the cylinder, directly under the edge of the stepped wear shoulder, the second - in the central part of the cylinder and the third - at a distance of about 10 mm above its lower cut.
Note. The block must be installed on the workbench strictly horizontally.
4. Repeat the measurements, this time in planes perpendicular to the axis of the crankshaft. Record the results of all six measurements and compare them with the requirements Specifications. If the difference in the diameters of any of the two cylinders is outside the allowable range, the cylinders are subject to turning, followed by the replacement of pistons with new ones of the appropriate repair size. The only alternative to turning cylinders is to completely replace the block complete with pistons.
5. Using the records of the results of measurements of piston diameters (see Section Removal, condition check and installation of connecting rod and piston assemblies), Calculate the piston clearances in the cylinders by subtracting these diameters from the cylinder diameters. Since the requirements for the fit of the pistons at the time of writing this manual are not specified by the manufacturers, seek advice from the specialists of the Skoda branded service center.
6. Lay the block on the workbench, crankcase down, and use a steel ruler and a blade-type feeler gauge to check the flatness of its mating surfaces. If the test results exceed those specified in Specifications valid value, the block can be machined (only for petrol engines) or replaced. On diesel engines, block turning is not possible.
7. Before assembling the engine, the cylinders should be honed.
8. Lightly lubricate the cylinder mirrors with clean engine oil to prevent corrosion. Wrap the block in a plastic bag and put it in a safe place before starting the assembly.