Note. In Skoda branded service centers, you can always order a remanufactured head, which often turns out to be much more practical than spending time and effort on performing rather complicated procedures for checking and restoring an old one.
Disassembly
Engines 1.3 l
1. Using a special tool, alternately compress the springs of each of the valves, removing the crackers of the split lock from their rods. When releasing the tool, remove the spring plates and the springs themselves from the valves (internal and external).
2. If, when the spring is compressed, the plate does not give in and does not release access to crackers, you should lightly tap on the tool mandrel with a light hammer.
3. Remove the outer and inner spring seats from the guide sleeve, then carefully remove the oil seal from the sleeve using pliers.
4. Remove the valve through the combustion chamber.
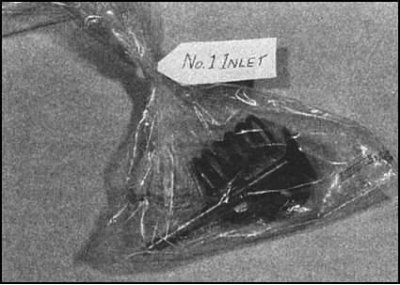
5. If the valves and related components are in satisfactory condition, the parts should be folded in the order they are installed on the engine, placing them in separate, specially marked bags.
Engines 1.6 l and diesel
1. On a diesel engine, remove the fuel injection nozzles and glow plugs (see chapters Supply system and Engine electrical equipment). Remove the coolant outlet elbow with gasket/O-ring.
2. On a 1.6 liter engine, unscrew the thermostat housing and oil pressure switch from the cylinder head.
3. Remove the timing belt gear from the camshaft stub.
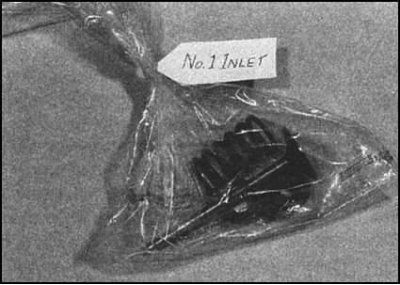
4. Prepare specially marked bags for folding in them the removed components of the valve mechanism. Installing components in random order will lead to accelerated wear of parts and premature failure of the entire mechanism.
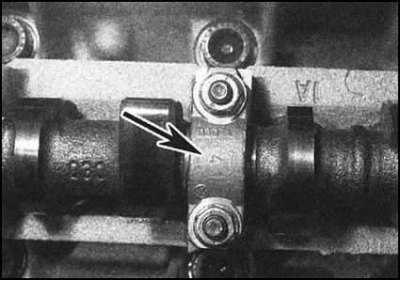
5. Check the camshaft bearing caps for factory markings. If necessary, mark yourself with a scriber or a center punch. Loosening the bearing cap nuts should be done gradually and evenly to avoid creating internal stresses in the shaft body. The procedure for loosening fasteners is described below.
6. Loosen the nuts on bearing caps Nos. 5, 1, and 3 first. Then move on to the 2nd and 4th bearing caps. Weakening is performed in a diagonal order in several steps (half a turn per approach) until it becomes possible to release the nuts manually.
Note. Lids are numbered sequentially (1 to 5) from the location of the timing belt.
7. Remove the old oil seal from the camshaft trunnion facing the timing drive. During assembly, the seal must be replaced without fail.
8. Gently, trying not to tilt, remove the camshaft from the head. Support the shaft at both ends and make sure that it is not caught by the cams and bearing journals on the protrusions in the body of the head.
9. Remove the hydraulic tappets from their seats and fold them in the order of installation on the engine, valve contact face down to prevent oil from escaping. Alternatively, the pushers may be placed in oil-filled containers. Keep in mind that random tappets during assembly lead to accelerated component wear and premature valvetrain failure.
10. Turn the head over and lay it sideways on the workbench. Using a special tool, alternately compress the spring of each of the valves and remove the crackers of the split locks. When "sticking" spring seats, tap on the upper jaws of the tool with a light hammer.
![]() | ![]() |
11. Release the tool and remove the top seat and spring itself.
12. Use pliers to remove the gland from the valve stem. Remove the valve from the head (from the side of the mating surface). If the valve is jammed in the guide sleeve, carefully grind its end surface with sandpaper. Proceeding in the same order, remove all remaining valves.
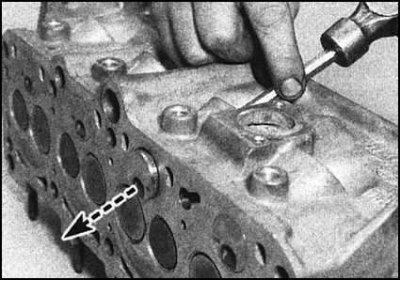
13. On a diesel engine, check the swirl chambers for burnouts and coking. If necessary, carefully knock out the defective chamber by inserting a drift into the hole of the corresponding nozzle.
Cleaning
1. Thoroughly flush the head with solvent, completely removing all traces of oil deposits. Particular attention should be paid to the condition of the camshaft journals, tappet sockets and valve guides. Carefully scrape off any traces of old gasket material from the head mating surface. Turn the head over and use a dull knife to remove carbon deposits from the surfaces of the combustion chambers and intake ports.
Attention! Try to prevent erosion of the working surfaces of the valve seats. Finally, flush the entire head with a suitable solvent, completely removing all traces of abrasive.
2. With a thin wire brush, clean the plates and valve stems, having previously scraped off the main mass of coal deposits from them with a blunt knife.
Attention! Try to prevent erosion of the working surfaces of the valve discs.
3. Using solvent, thoroughly wipe all other removed components. Then dry them thoroughly. Prepare replacement seals / oil seals.
Status check
Head casting
Note. Repair of valves and diesel head is not possible (except for lapping). In case of damage or wear, the components must be replaced.
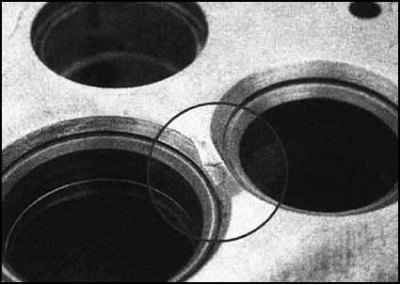
1. Carefully inspect the head casting, checking it for cracks in the area of the mounting holes, valve seats and spark plug niches. In case of detection of defects in the jumpers between the seats of adjacent valves, contact the car service specialists for advice.
2. Check up a condition of working facets of saddles of valves. Minor defects can be corrected by lapping the valves. In case of revealing deep cavities, cracks, traces of burnout and other serious defects, the restoration of the head becomes possible only in the conditions of a car service workshop.
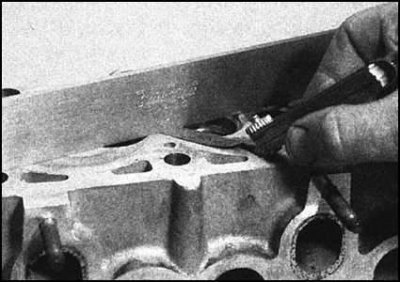
3. Check up flatness of surfaces of interfacing of a head with the block, the inlet pipeline and a final collector. Take measurements along the diagonals of the surfaces. Compare results with requirements Specifications. On gasoline engines, it is possible to eliminate minor non-flatness with sandpaper.
4. Requirements for the minimum allowable cylinder head height are also given in Specifications. When performing head turning, keep the following points in mind:
- a) Turning the head is only allowed while maintaining the minimum installation height (if so, see Specifications);
- b) Upon completion of the groove, the mating surfaces must also be chamfered on the valve seats, bringing them in line with the new height of the head. Failure to do so may result in component damage due to impact of valves against piston crowns;
- c) Before turning valve seats, make sure that there is enough material left to complete the repair. Removing a layer of excessive thickness can lead to too much protrusion of the valve stems above the ends of the guide bushings and, as a result, to a malfunction of the hydraulic tappets. Consult with experts.
Attention! For some engine modifications, replacement valves of a shorter length can be purchased - contact Skoda branded service centers.
Camshaft - 1.6L and Diesel engines
Note. A description of the procedures for removing and installing the camshaft on 1.3 l models is given in Section Removal and installation of the timing belt and its covers.
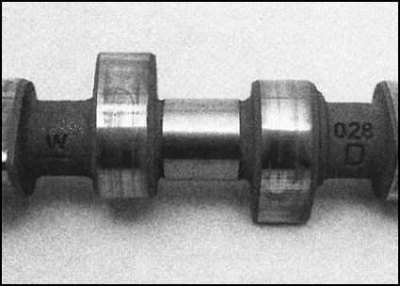
1. The camshaft has an identification marking in the form of marks stamped on its sides between the intake and exhaust valve drive cams. The decoding of the marking can be performed by specialists of the Skoda branded service center.
2. Perform a visual check of the camshaft for signs of wear and other defects on the working surfaces of the cams and necks. Surfaces should be absolutely smooth and have a slightly dull finish. The presence of scratches, scuffs, cavities or areas polished to a shine indicates the approaching end of the shaft's service life. As soon as the case hardening layer is damaged, the shaft wears quickly and should be replaced if such signs are found.
Note. If cams are found to be defective, also check the condition of the contact surfaces of the corresponding hydraulic tappets.
3. On diesel engines, check the vacuum pump drive gear for wear.
4. If there are signs of overheating of the treated shaft surfaces (discoloration or bluish coloration), a possible malfunction of the lubrication system should be assumed. Overheating often leads to deformations of the shaft, so the amount of its runout should be determined. Place the shaft with the trunnions in the recesses of the two V-blocks and use a plunger-type dial gauge to measure the amount of runout on the center journal. If the measurement result exceeds the specified Specifications permissible value, the shaft must be replaced.
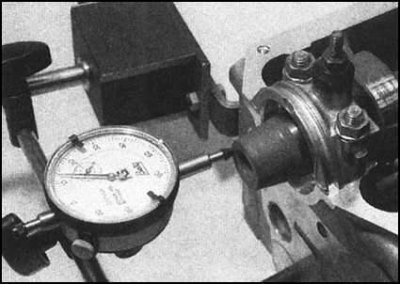
5. To assess the axial play of the camshaft, temporarily place it back into the cylinder head and install the covers of the first and last bearings, tightening their fixing nuts with the required force. Mount the dial gauge on the side of the front pin of the shaft (facing towards the location of the timing belt), parallel to the axis of the shaft. Push the shaft all the way back (towards the flywheel), press the meter plunger against the end of the front pin and zero the instrument. Now move the shaft forward for the full length of its stroke and take the meter reading. Verify that the test is correct by moving the shaft back again and making sure that the gauge pointer has returned to zero.
Note. Checking the axial play of the camshaft should be carried out with the hydraulic valve lifters removed from the head.
6. Compare the test result is out of range specified in Specifications allowable range, you should consider options for the upcoming replacement of the head, shaft and its bearing caps - contact a car service specialist for advice.
7. The difference between the diameters of the bearings and the shaft journals determines the size of the working clearances in the bearings and should also not go beyond the allowable range.
8. The diameter of the shaft journals is not specified in any way by the manufacturers, which is why the compilers of this Guide do not recommend this check by direct measurements using a micrometer and a bore gauge.
9. A more appropriate way to evaluate bearing clearances in this case is to check with a special Plastigauge kit. The size of the gap is determined by the degree of flattening of pieces of soft calibrated wire from the set when it is compressed between the working surfaces of the bearings and the shaft journals. Measurement of the width of the flattened pieces of wire is carried out according to the scale printed on the packaging of the set.
10. Below is a detailed step-by-step description of how to perform this test. It should be noted that the same method is the basis for determining the working clearances in the main and connecting rod bearings of the crankshaft (see Section Removal and installation of a head of cylinders in gathering with the inlet pipeline and a final collector).
11. Make sure that the working surfaces of the camshaft, cylinder head and bearing caps are absolutely clean and dry. Install the shaft in its regular place in the head.
12. Lay pieces of calibrated wire from the set along the necks of the shaft.
13. Lightly lubricate the bearing surfaces of each of the caps with a special silicone compound to prevent wire sticking. Install the covers in their places and tighten the nuts of their fastening with the required force (see instructions in subsection "Assembly").
Note. If stepwise tightening of fasteners is provided, tighten the nuts with a force of only the first stage. Do not rotate the shaft after installing the covers.
14. Carefully remove the covers, lifting them vertically so as not to disturb the shape of the flattened pieces of wire. If the wire, despite the measures taken, sticks to the working surfaces of the covers, the procedure will have to be repeated.
15. Using the scale printed on the package, measure the width of the flattened pieces of wire. The graduation of the scale is such that the reading taken is directly equal to the value of the determined gap.
16. Compare your results with the requirements Specifications. If the gaps are out of tolerance, the camshaft and cylinder head must be replaced. Note that in Skoda branded service centers you can order a repair size camshaft with a set of corresponding liners, but only complete with a replaceable head.
17. Finally, remove the shaft and remove all traces of flattened gauge wire from its necks and working surfaces of the covers by carefully scraping them off with the edge of a credit or payphone card. Then wipe the surfaces, finally clearing it of silicone residues.
Valves and related components
Note. On none of the engines, the groove of the valve plates is not provided. The only acceptable way to restore the quality of the seal is to lap the valves to their seats. If a satisfactory result cannot be achieved by such lapping, the valves should be replaced.
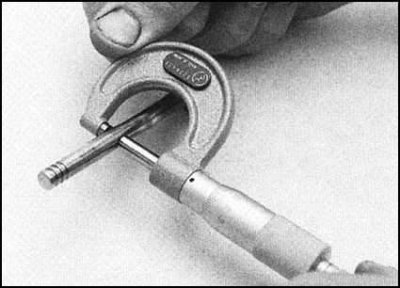
1. Carefully inspect each valve for wear. Check the valve stems for signs of stepped wear, scratches, scuffs and other mechanical damage. Using a micrometer, measure the diameter of each rod in several places.
2. Check the valve discs for cracks, cavities and traces of burnout. Minor defects can be eliminated during the lapping process (see below), in case of more serious wear, the valves must be replaced.
3. Check up a condition of end surfaces of cores of valves. The presence of deep cavities and other defects of this kind on them may be due to a malfunction of the hydraulic pushers (engines 1.6 l and diesel).
4. Alternately laying the valves in the V-shaped block, using a dial gauge, evaluate the amount of runout of their plates. Permissible values are not specified by manufacturers, however, if the runout is noticeable, the defective valve should be replaced.
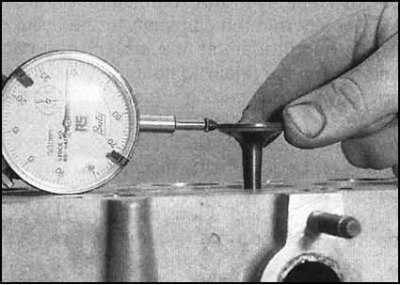
5. After filling the valve into the appropriate guide sleeve, again using a dial gauge, evaluate the size of its seat clearance. The end of the valve stem during the measurement must be flush with the top cut of the sleeve.
6. If there is excessive valve play in the sleeve, both components (and valve and sleeve) are to be replaced.
Note. The preload guide bushings are seated in their sockets in the cylinder head and a hydraulic press is required to remove them, which is why it would be better to entrust this work to the specialists of the service station.
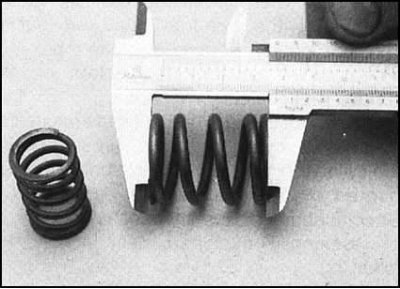
7. Using a vernier caliper, measure the free length of each valve spring. Since the lengths of the springs are not specified by the manufacturers, the only way to check their condition is to compare the measurement results with the length of a new spring. The compilers of this manual recommend replacing valve springs during an engine overhaul, regardless of their condition.
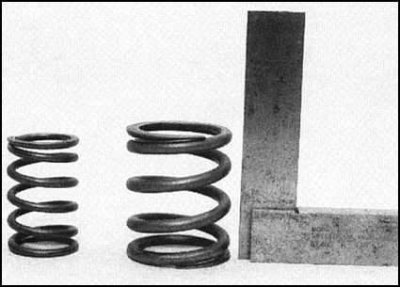
8. Having installed the spring vertically, evaluate the quality of its trimming. Replace if necessary.
9. When loading the valves with special weights, evaluate the magnitude of the force developed by the springs. It is better to entrust the performance of this check to the specialists of the service station. The installation of sagging springs leads to an increase in the overall noise background of the engine and a decrease in compression pressure in the cylinders.
Lapping of valves
1. Restoration of the lost tightness of the closing of the valves is carried out by grinding them to their seats. Lapping is done using several grades of lapping paste and a valve gripper with a suction cup.
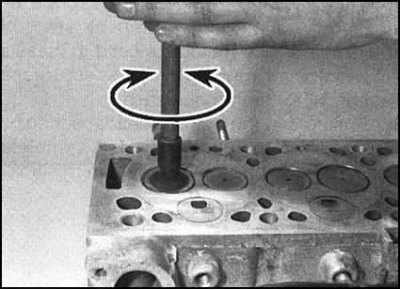
2. Apply a small amount of fine grinding paste to the sealing surfaces of the cylinder head. Turn the head upside down and insert the valve into the appropriate guide bushing. Fix the suction cup of the gripper on the plane of the valve disc and start with reciprocating rotational movements and grind it with a working chamfer to the seat. Raise the valve from time to time to redistribute the paste.
3. Continue lapping until a continuous matte polished ring of uniform thickness appears on the face of the seat bevel. Repeat the procedure for each of the remaining valves.
4. In case of severe damage to the working chamfers, lapping should begin with the use of a coarse-grained paste at the first stage, gradually moving to finer gradations. First you need to make sure that the residual thickness of the plate and seat allows for a sufficiently deep lapping. On 1.6L models and diesel engines, when removing an excessively thick layer of material, there is a risk of too much protrusion of the valve stems over the sections of the guide bushings, which is fraught with a malfunction of the hydraulic tappets. Before starting grinding, consult with car service specialists.
5. Upon completion of the first stage of lapping (with coarse paste) thoroughly wash off traces of abrasive with a solvent, then go to a finer paste.
6. After lapping, flush the head and valves with solvent and dry the components thoroughly.
Assembly - engine 1.3 l
Attention! When using old components, install them on the engine strictly in the same order. This condition also comes into force after the completion of the grinding of new valves - they must be installed in the head strictly in those seats to which they were rubbed.
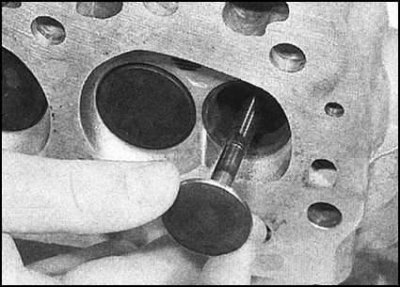
1. Lubricate the valve stems and thread them into their respective guide bushings.
2. Starting with the first valve, place the seats on the first valve, first the inner, then the outer springs.
![]() | ![]() |
3. Lubricate the oil seals with clean engine oil and install them on the guide bushings (branded Skoda caps are equipped with special plastic protectors that are used when putting the cap on the valve).

4. Place the cap on the stem and place it on the guide bush. Take care not to damage the jaws of the cap while lowering it along the valve stem.
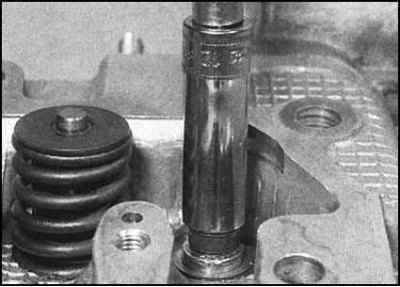
5. Using an appropriately sized socket or a piece of pipe of the appropriate diameter as a mandrel, fit the cap firmly onto the sleeve. If used, remove the plastic protector from the end of the valve stem.
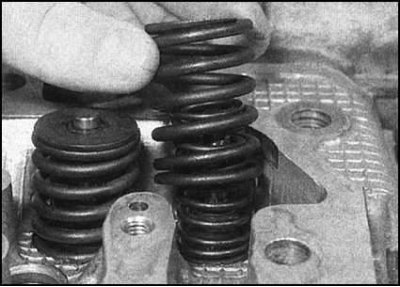
6. Place your inner and outer springs on your saddles),...
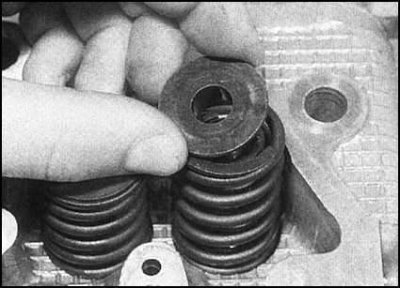
... put on the retainer plate from above.
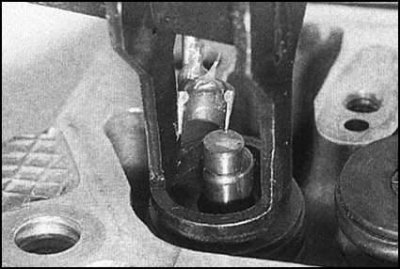
7. Using a special tool, compress the valve springs and fit the crackers of the split lock into the groove on the shaft.
Note. A small amount of grease applied to the inside of the nut will help to temporarily hold the nut in place before releasing the tool. Release the tool and repeat the procedure for the remaining valves.
8. When you have finished installing all the valves, lay the head on a workbench and tap it with a hammer through a block of wood to shrink the components.
9. Install the head on the cylinder block (see part Repair without removing the 1.3 l petrol engine from the car this Chapter).
Assembly - engines 1.6 l and diesel
Attention! When using old components, install them on the engine strictly in the same order. This condition also comes into force after the completion of the grinding of new valves - they must be installed in the head strictly in those seats to which they were rubbed.
1. On diesel engines, if removed, with hammer blows through a wooden block, plant the swirl chambers perpendicularly into their nests. Pay attention to the presence of guide grooves in the sockets.
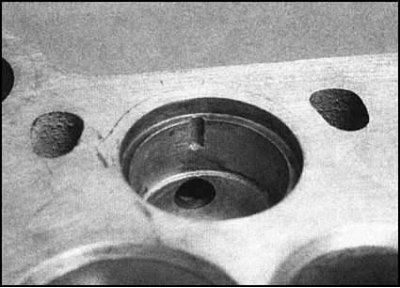
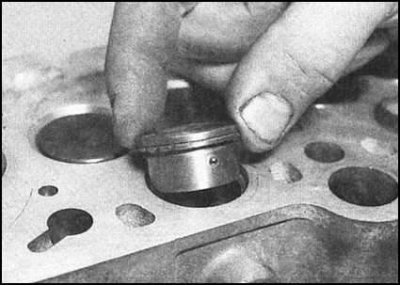
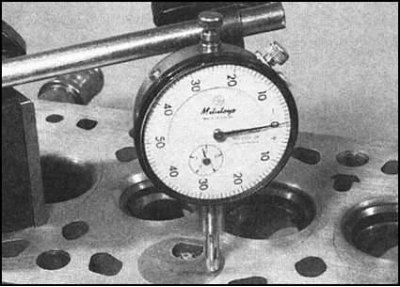
2. Using a dial gauge, determine the amount of protrusion of the vortex chambers above the surface of the head. If the measurement results exceed those specified in Specifications permissible value, the head should be specially machined in a car service workshop in order to prevent the risk of damage to the chambers as a result of contact with the pistons.
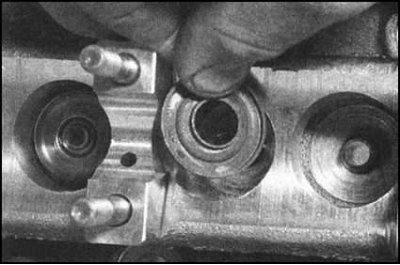
3. Turn the head over and place it on a couple of wooden blocks. Where required, first install the lower spring seats with the convex side towards the head.
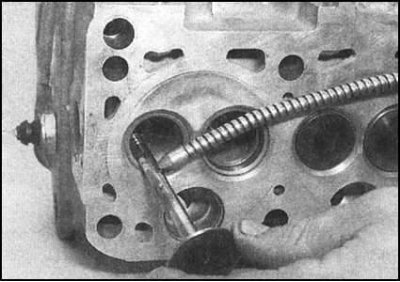
4. By lubricating the valve stems with clean engine oil,...
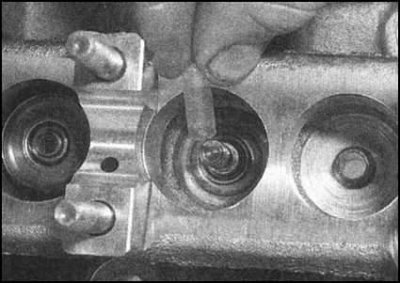
...install them one by one in their respective guide bushings. Put a special plastic protector on the end of the stem of the first of the valves.
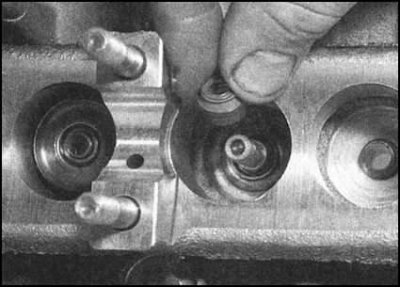
5. Lower the oil deflector cap into clean engine oil and, putting it on the rod,...
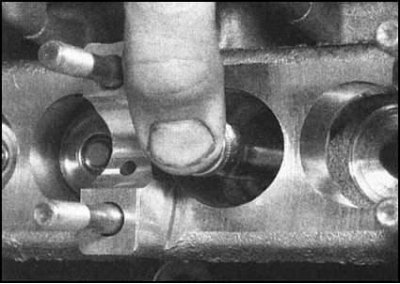
...tightly seat on the guide sleeve. Use a suitable size deep socket as a mandrel.
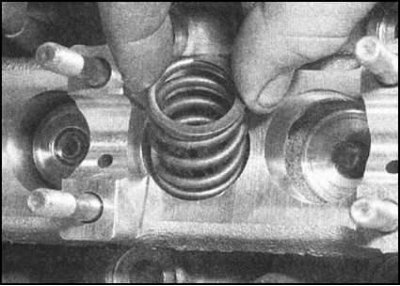
6. Put the spring on the valve stem.
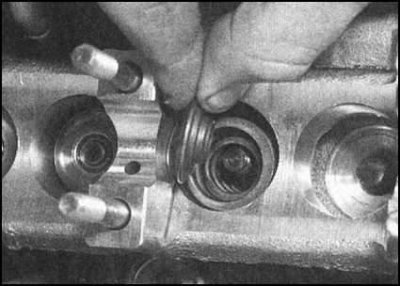
7. Install the upper saddle on top of the spring,...
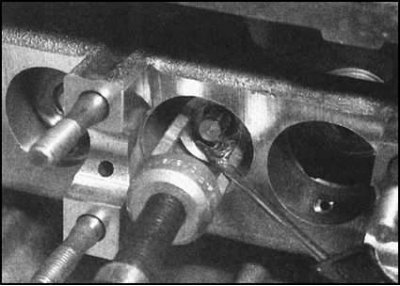
...then compress the assembly with a special tool and install it into the groove on the split lock rods.
8. Repeat the procedure for the remaining valves. To shrink the components, tap the ends of the valve stems with a soft-faced hammer, then make sure that the upper spring seats are securely held by crackers.
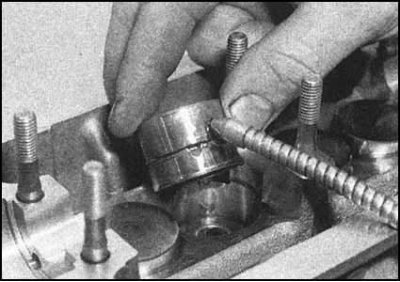
9. Lightly lubricate the walls of the hydraulic tappets with clean engine oil and install them in their sockets in the head. Push the tappets into their sockets until they rest against the valve stems, then lubricate the surfaces in contact with the camshaft lobes.
10. Lubricate the crankshaft journals and bearing surfaces in the head with clean engine oil, then carefully place the shaft in its proper place. Hold the shaft firmly by the ends and try not to damage its necks and cams.
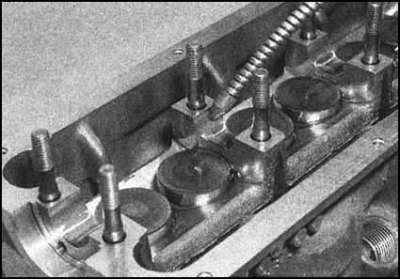
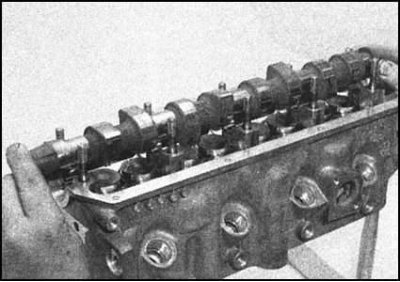
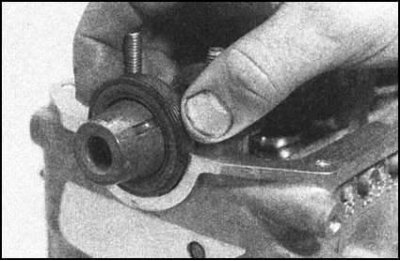
11. On diesel models, lubricate the sponges of the new oil seal with clean engine oil and put it on the crankshaft trunnion. Advancing the oil seal along the trunnion, seat it in the lower half of your housing in the head (see part Repair without removing the diesel engine from the car).
12. Grease the top part of necks of a camshaft and establish on them covers of bearings.
Petrol engines 1.6 l

1. Make sure the orientation of the camshaft bearing caps is correct. The covers should be deployed with wider projections of the casting towards the inlet of the head. The identification marking must be readable when looking at the head from the outlet side.
2. Reinstall the 2nd and 4th bearing caps and tighten their fastening nuts diagonally to the first stage torque.
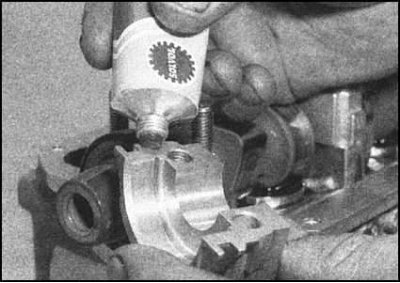
3. Lubricate the mating surfaces of the 1st and 5th bearing caps with sealant. Replace the 1st, 3rd and 5th covers and tighten the fixing nuts to 1st stage torque.
4. Working diagonally, tighten the fasteners of all caps to the angle of the second stage of tightening (use a goniometer or a template specially made of thick cardboard).
5. Screw in bolts of fastening of a cover of the 5th bearing and tighten them with the demanded effort.
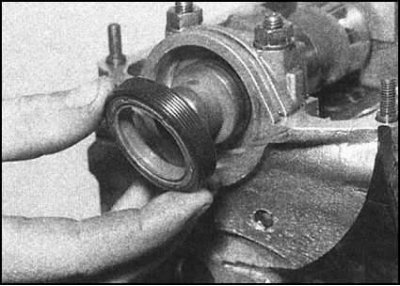
6. Grease sponges of a new epiploon with pure impellent oil and put on it on a camshaft pin. Using a suitable size deep socket as a mandrel, tap the gland perpendicularly into the socket in the casing until it stops against the internal stop (see part Repair without removing the 1.6 l petrol engine from the car this Chapter).
7. Reinstall the thermostat housing and the engine oil pressure switch.
Diesel engines
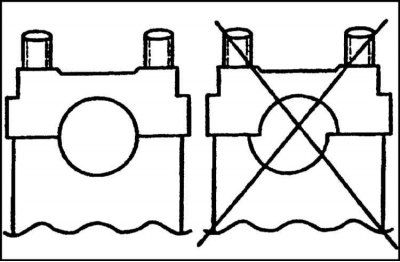
1. Mounting holes are drilled in the covers asymmetrically, which determines the uniqueness of the installation of the latter.
2. When installing the bearing caps, the camshaft must be turned by the working projections of the cams of the valves of the first cylinder up.
3. Fit the 2nd and 4th bearing caps and diagonally tighten them evenly to the correct torque.
4. Now install the covers of the 1st, 3rd and 5th bearings. Tighten the fixing nuts to the required torque, then make sure that the 5th bearing cap is properly seated by lightly tapping the end of the camshaft.
5. Install the coolant pipe, replacing its gasket/o-ring if necessary.
6. Reinstall the fuel injection nozzles and glow plugs.
All engines
1. In accordance with the instructions given in Parts Repair without removing the 1.6 l petrol engine from the car, Repair without removing the diesel engine from the car of this chapter, perform the following procedures:
- a) Reinstall the camshaft gear;
- b) Install the intake manifold and exhaust manifold with new gaskets.
2. Install the head on the cylinder block (see part Repair without removing the 1.6 l petrol engine from the car or Repair without removing the diesel engine from the car this Chapter).