Gearbox - appearance
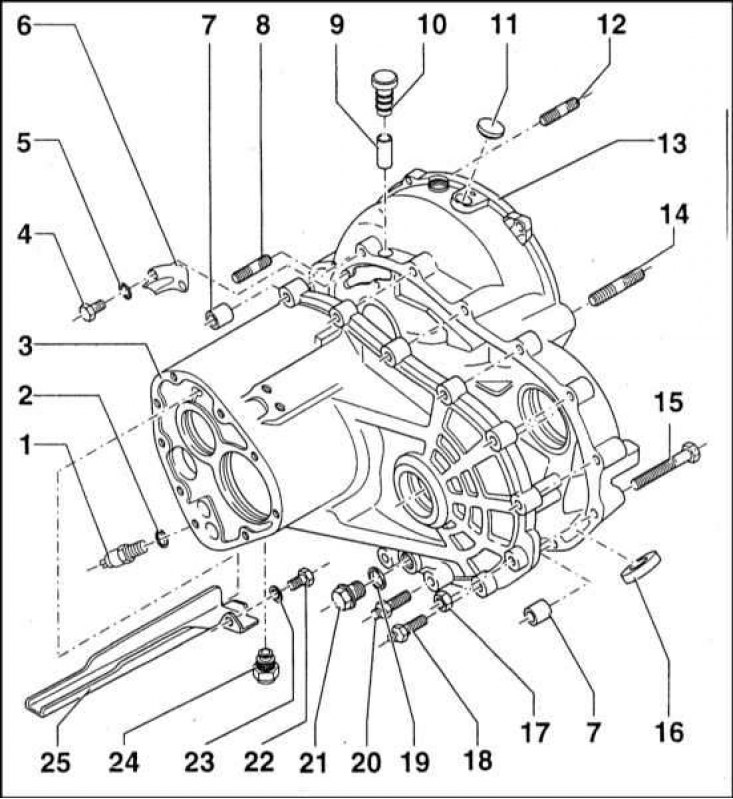
1 - Sensor-switch of reversing lights; 2 - O-ring; 3 - Gearbox housing; 4 - Screw (10 Nm); 5 - Lock washer; 6 - Visor; 7 - Guide pin; 8 - Stud M10 (50 Nm); 9 - Ventilation tube; 10 - Cork; 11 - Plug; 12 - Hairpin (50 Nm); 13 - Carter (dome) clutch; 14 - Hairpin (50 Nm); 15 - Screw; 16 - Magnet; 17 - Nut (35 Nm); 18 - Screw (25 Nm); 19 - O-ring (must be replaced during assembly); 20 - Threaded drain plug (60 Nm); 21 - Screw (10 Nm); 22 - Thrust ring; 23 - Stop screw (35 Nm); 24 - Cork; 25 - Oil chute
Assembly of the gearbox (checkpoint) placed in a cast aluminum crankcase, bolted to the left end of the engine. The assembly includes the mechanisms of the gearbox itself, as well as the final drive differential.
Rotation is transmitted from the engine crankshaft through the clutch assembly to the input shaft of the manual transmission, equipped with an elongated and splined trunnion, which is threaded into the hub of the clutch friction disc. The input shaft of the box rotates in non-separable ball bearings placed in a sealed housing. From the input shaft, rotation is transmitted to the secondary shaft of the box, the right end of which is threaded into a roller bearing, and the left end into a sealed ball bearing. The output end of the secondary shaft of the box is engaged with the crown driven gear of the main gear, rigidly connected to the differential box, inside which the planetary assembly is located. From the side gears of the differential, the rotation is transmitted further to the drive shafts and then to the front drive wheels of the vehicle. The pinion gears are loose on their axis, which makes it possible to rotate the driving wheels of the vehicle at different speeds, thereby completely eliminating the possibility of slipping of the inner wheel during maneuvers.
The primary and secondary shafts of the gearbox are parallel to each other, as well as parallel to the crankshaft and drive shafts of the drive axle. Due to the particular configuration, the gears of both shafts are constantly engaged with each other. In neutral gear, the gears rotate freely on the output shaft, not transmitting rotation to the main gear driven gear.
Gear shifting is carried out using the manual transmission control lever installed on the floor of the passenger compartment and through the gear selection drive mechanism. The drive of the gear selection mechanism consists of a set of shift forks, with the help of which the sliding clutches of the synchronizers move along the shaft, blocking the gears of the corresponding gears with their hubs. Since the hubs of the sliding clutches are equipped with splines that engage with the mating splines of the output shaft, the gear locked on the hub begins to rotate with the shaft, providing further drive with the appropriate gear ratio. To guarantee the speed and quality of gear shifting, the gearbox provides synchronization of all forward gears. Synchronization is provided by the use of locking rings with spring-loaded sliding keys and synchronizer hubs with gears. Synchronizer cones provide mating surfaces for the locking rings to the gears. The principle of design and operation of the manual transmission is described in more detail in Section System design, description of individual components and mechanisms.