Drive shaft design
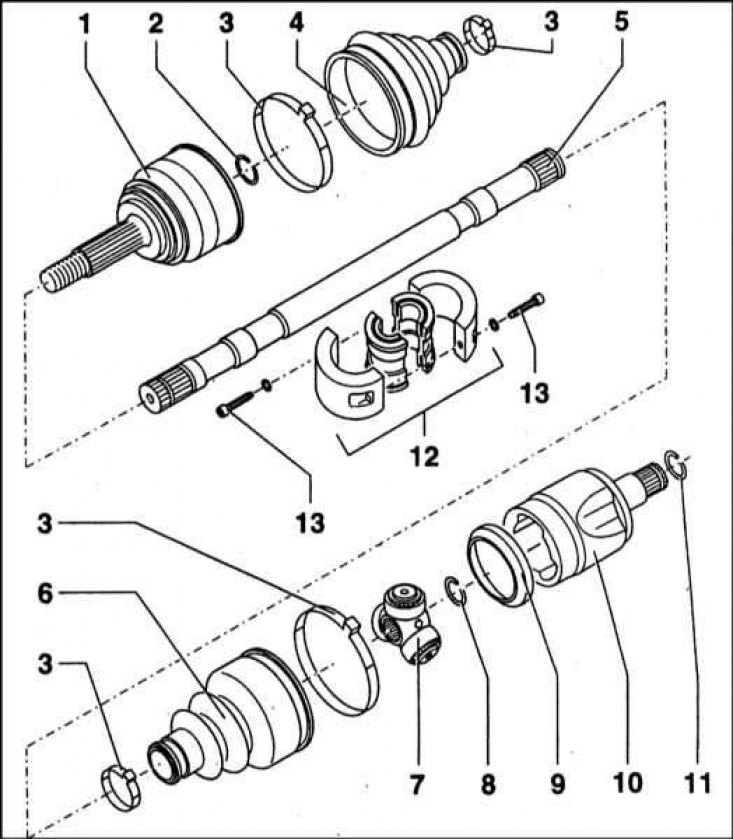
1 - Outer CV joint; 2 - Retaining ring; 3 - Bandage tape for fastening the protective cover; 4 - Protective cover; 5 - Drive shaft; 6 - Protective cover; 7 - Crosspiece of the tripod assembly of the outer CV joint; 8 - Retaining ring; 9 - Thrust ring; 10 - Outer clip of the CV joint; 11 - Retaining ring; 12 - Vibration damper (vibration damper) right drive shaft; 13 - Bolt with an internal hexagon for a bar key
The transmission of rotation from the transmission final drive differential to the drive wheels is carried out by means of two solid forged steel drive shafts. The outer ends of both drive shafts are equipped with splines mating with the splines of the hubs of the driving wheels of the vehicle. A large nut is used to secure the shaft to the hub. The inner ends of the shafts also end with splined trunnions, which mate with the side gears of the differential. The left shaft is shorter than the right one due to the asymmetry of the location of the main gear relative to the longitudinal axis of the vehicle. The composition of the right (longer) a vibration damper is included, located at a distance of 105 mm from the edge of the protective cover of the inner CV joint, and designed to dampen torsional vibrations of the assembly during its rotation. The design of the drive shaft is shown in the accompanying illustration. After forging, the drive shafts are hardened in a special way, which gives them increased strength.
Equal velocity hinges are installed at both ends of each shaft (SHRUS). The hinges provide stability and smooth rotation of the drive at any angle of the wheels, due to the relief of the road surface, as well as during cornering. Cage ball bearing assemblies are used as external CV joints. Internal hinges have a tripod design.